Creation of safe working conditions
Management of labor protection and industrial safety issues
The priority of Samruk-Energy JSC is strict compliance with industrial safety rules and norms, ensuring safe working conditions for both personnel and contractors during production activities. We act in accordance with the requirements of the legislation of the Republic of Kazakhstan and voluntarily undertake obligations in accordance with the international standard ISO 45001.
At Samruk-Energy JSC, we make every effort to create a safe labor environment, promote safety culture among personnel, maintain a healthy lifestyle, and introduce advanced technologies. We aim to exclude accidents and incidents, striving to ensure safety and comfort in the workplace for all our employees.
HSE goals of Samruk-Energy JSC:
- improving the efficiency of business processes through continuous development of the corporate management system;
- compliance with all applicable health and safety regulations and requirements defined by legislation and international standards;
- guaranteeing safe and comfortable working conditions, reducing risks to the health of personnel and all stakeholders by preventing and eliminating possible hazards;
- using modern equipment, innovative technologies and protective equipment to ensure workplace safety;
- organizing consultations with employees and ensuring their active participation in health and safety processes.
In the reporting period, we continued our efforts to implement our strategy and objectives in the field of occupational health and safety. However, realizing the constantly changing conditions and requirements, we concluded that it is necessary to revise our strategy and policy in this area.
As a result of the analysis and discussions, an Action Plan to achieve zero injuries in the Group of companies of Samruk-Energy JSC was developed, including:
- Improvement of the occupational health and safety management system to increase its effectiveness. The measure will be achieved through ensuring transparency of incident reports to prevent serious consequences such as fatalities and accidents;
- Improving safety culture by involving personnel in the occupational health and safety management system and improving monitoring of its effectiveness by applying international standards.
Principles and rules of Samruk-Energy JSC policy on reduction of occupational injuries and improvement of personnel working conditions are mandatory for all employees and contracting organizations.
Occupational health and safety management system
The management system in the field of occupational health and safety in Samruk-Energy JSC applies to all employees of the Company and personnel of contracting organizations. The system is based on the legislation of the Republic of Kazakhstan, principles of Samruk-Energy JSC in the field of labor protection, and other internal corporate documents.
Key regulatory documents defining the principles and rules in the field of occupational health and safety of the Company:
- Policy of Samruk-Energy JSC of the corporate management system of the Group of companies of Samruk-Energy JSC;
- Regulations on Transportation Safety Management in the Group of companies of Samruk-Energy JSC;
- Development Strategy of Samruk-Energy JSC for 2022-2031;
- Standard “Assessment of Industrial Safety and Labor Protection Risks”;
- Standard “Motivation of Personnel to Safe Behavior”;
- Standard “Accounting and Investigation of Accidents”;
- Standard “Assessment of Occupational Health and Safety Management System”.
Occupational health and safety issues are managed at all levels of the Company.
List of information on industrial safety service of Samruk-Energy JSC
Name of required data | Indicator* |
---|---|
Number of specialists in the central/ office/corporate PC center: |
3 |
- occupational health | 3 |
- occupational safety | 3 |
- fire safety | - |
- other areas | - |
Number of specialists in subsidiaries and affiliates | 85 |
- occupational health | 40 |
- occupational safety | 23 |
- fire safety | 11 |
- other areas | - |
Ratio of employees of occupational safety services to one employee of the Company |
The total number of employees covered by the occupational health and safety management system is 17,071. Number of full-time employees covered by the HSE management system, who passed internal audit 100%, which is 17,071. Number of non-staff employees covered by the HSE management system, who passed internal audit — 100%, which is 3,914. Number of specialists — 85. The ratio of employees of OHS services to one employee — 200. |
* Note. Environmental protection employees are not counted.
The Director for HSE (Health, Safety and Environment) reports directly to the Chairman of the Company's Management Board and is responsible for the overall coordination of work to improve the occupational safety system both in the Company itself and in its subsidiaries.
The head of the division responsible for HSE issues performs the functions of preventing violations of HSE norms and rules, promptly responding to incidents, and monitoring, analyzing and controlling risks in this area. Occupational safety services in subsidiaries are managed by the first manager. To ensure efficiency and prompt implementation of necessary changes to the occupational health and safety management system, we regularly analyze the qualifications composition of the personnel of the occupational safety services in the Company's subsidiaries.
Quarterly meetings are held with the active participation of the Chairman of the Management Board, Chief Directors and top managers of subsidiaries to improve safety culture, prevent accidents, and reduce injuries.
Committees responsible for occupational health and safety conduct detailed analysis of issues in these areas and monitor the effectiveness of measures. The Board of Directors and the Management Board review and approve reports on occupational safety and risk management based on the information provided by the Committees. In addition, the Committees ensure compliance with confidentiality requirements.
During the reporting period, each of the Committees held four meetings to discuss quarterly reports on work in the field of occupational safety and health, as well as data on occupational injuries.
In 2023, Occupational Safety and Health Production Councils throughout the Group of companies of Samruk-Energy JSC held 36 meetings attended by both employer representatives and personnel representatives, including technical inspectors for occupational safety.
Labor Protection, Industrial Safety and Environmental Protection Management System of Samruk-Energy JSC
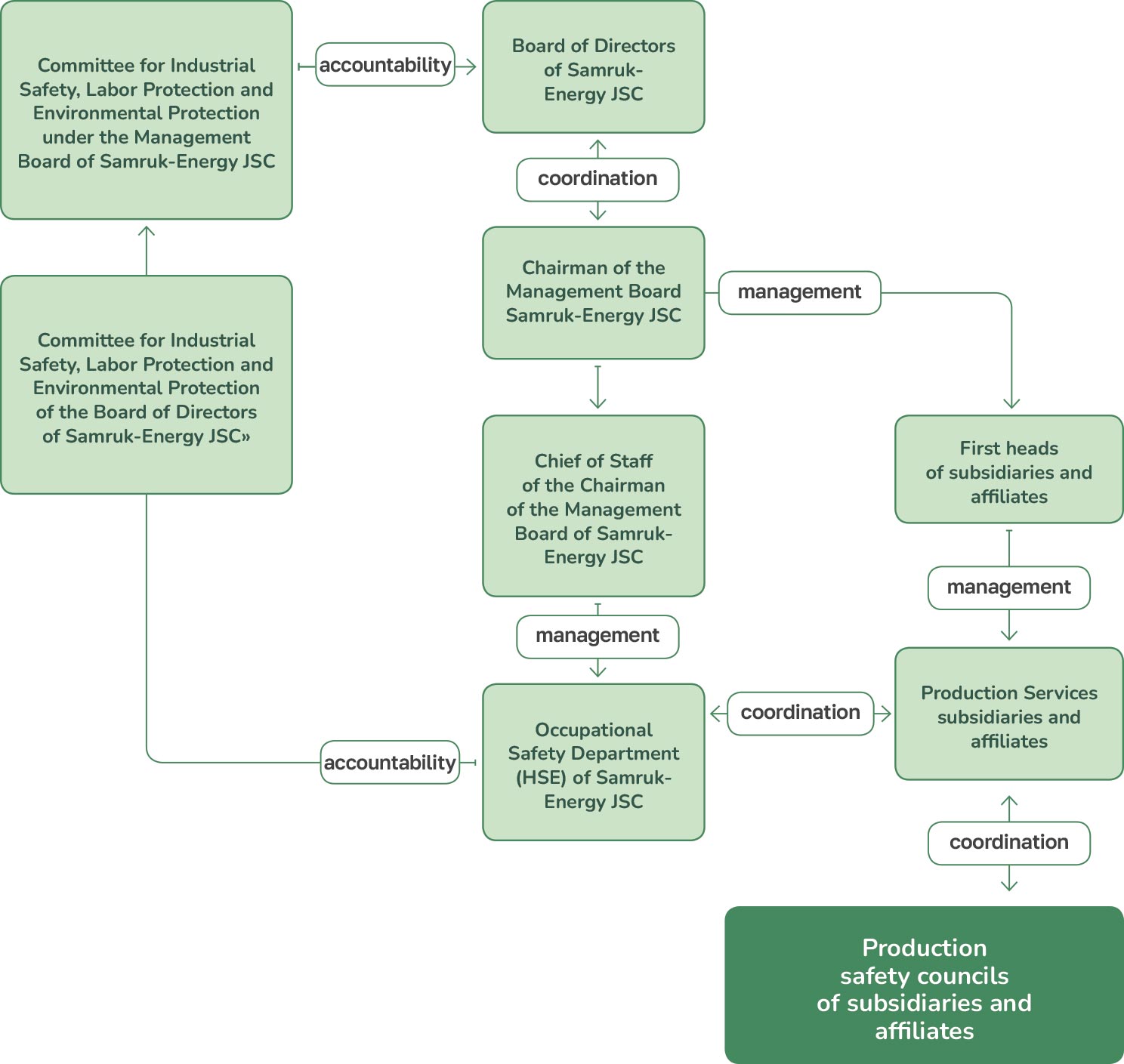